The laser cutting production process of laser cutting machines is widely used in manufacturing and production. Compared with traditional cutting methods, laser cutting machine is faster and more accurate. It mainly uses a high-power laser beam to heat the necessary cutting positions, instantly vaporizing the raw materials to achieve the desired cutting effect. During cutting, there may be slag hanging on the workpiece. What is the reason? Let’s take a look.
What is the reason for slag hanging after cutting by laser cutting machine?
When processing sheet metal with fiber laser cutting machines, a significant amount of heat is generated. Under normal conditions, the heat generated by cutting will be adequately dissipated through cooling in the processed sheet metal. In small circular hole processing with fiber laser cutting machines, there will be sufficient cooling on both sides of the hole; however, for inner holes within double holes where space for heat dissipation is limited, excessive concentration of energy can lead to slag hanging.
In addition, when cutting thick steel plates, deposition of molten metal on the surface layer and accumulation of heat can disrupt auxiliary gas flow and result in excessive slag hanging.
These occurrences can seriously affect product precision and appearance quality and easily lead to customer dissatisfaction. Many beginners in laser field are not clear about how to deal with slag adhesion caused by metal laser cutting machine processing.
In fact, slag adhesion during laser production processes depends on factors such as processing standards set up for different materials:
1. Carbon steel: If the production and processing standards are set appropriately, there will be very few instances of slag sticking. Slag sticking may occur during thick steel plate cutting, but it is easily eliminated.
2. Galvanized sheet: The frequency of slag sticking is high, and the standard range for conducting high-quality cutting is narrow. In the production and processing of raw materials coated with topcoat, it is necessary to first carry out the production and processing of cutting off the wiping layer, and then carry out the construction technology of cutting raw material production and processing.
3. Stainless steel sheet: When assisting the gas is O2, it is difficult to prevent the generation of slag, and the generated slag is also somewhat hard and difficult to remove. Applying N2 in the production and processing of non-air oxidation laser cutting can significantly reduce the amount of slag.
4. Aluminum: In the cutting of aluminum profiles, the thicker the parts, the more slag will be generated.
How to solve it?
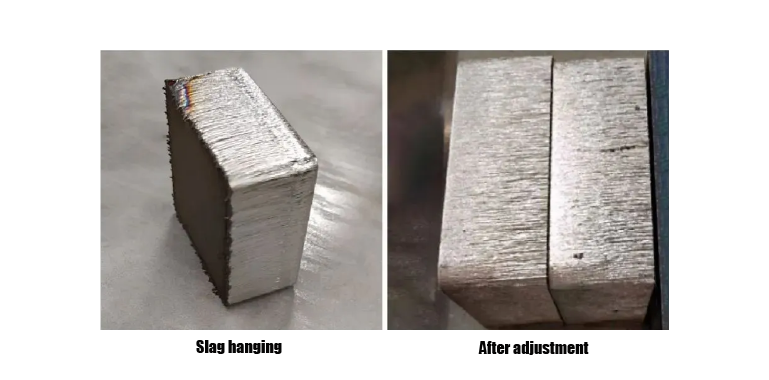
After slag hanging occurs in cutting, first find out the causes from the following points, and then adjust them to solve the generation of slag hanging:
1) Focal point position: The distance between focal point position and workpiece surface affects roughness of the cross-section, inclination of the kerf, total width, and adhesion of molten slag. If the focal point position is too advanced, it will increase heat absorption by the workpiece below resulting in melted material flowing as liquid around the cut and adhering to its lower surface after cooling. On the other hand, if it is too backward, less heat will be absorbed by the workpiece below causing incomplete melting and resulting in sharp short slag adhering to the lower surface.
2) Cutting speed: The selection of cutting speed depends on material type and thickness. Different cutting speeds can have a significant impact on cutting quality. Too fast cutting speed may cause inability to cut or sparks splattering while too slow cutting speed may result in over-melting of materials leading to rougher cross-sections.
3) Output power: The selection of laser output power affects cutting quality. Output power should be determined based on material type and thickness. Insufficient output power may prevent effective cutting while excessive output power can lead to excessive melting with larger kerfs.
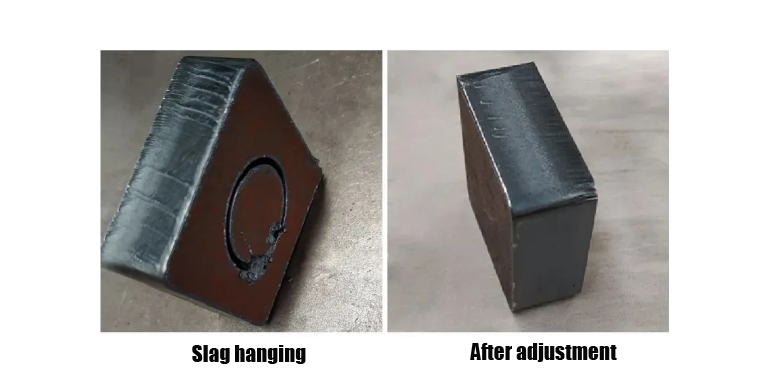
4) Assist gas pressure: Proper assist gas pressure helps remove molten slag during cutting process and cools down thermal hazards caused by laser heating. The choice of assist gas (such as O2 for most metals or rare gases for some non-metallic materials) depends on specific requirements for different materials.
Fiber laser cutting machines are highly precise equipment where even slight incorrect data input can cause operational abnormalities; therefore, strict attention should be paid during operation to minimize errors.
So we should be cautious when operating a laser cutting machine in actual practice, based on the characteristics of the raw materials. By making reasonable adjustments, the efficiency and precision of laser cutting can be improved, the slagging rate can be reduced, and product quality can be enhanced.